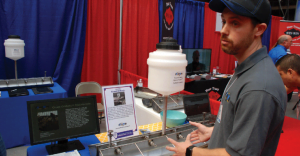
Story by Kevin Schulz
An esteemed panel of judges chose eight products from the World Pork Expo New Product Tour as finalists.
Farmers have always been good at seeing a problem, and rather than waiting for someone else to fix it, they find the solution themselves. Roy Winkler fits that mold.
Winkler, a wean-finish production manager with Haverkamp Brothers at Bern, Kan., was tired of seeing weaned pigs fall back and he sought a better way to save more of the challenged pigs in their fallback pens. The result: the Gruel-O-Matic Rescue Feeder from HavWin LLC that allows feedstuffs to be put in a feed tray, which also has nipple waterers so the piglets can mix gruel to their own desired consistency.
Spring-loaded fasteners anchor the feeder securely to the floor. There are two models: a larger model with two feed trays and four nipple waterers for each tray, and a smaller unit with two feed trays and two nipple waterers for each tray. The larger model accommodates about 50 to 60 head; the smaller unit works with 25 to 30 head.
A poly tank attached to the system can administer water, electrolytes and antibiotics to the pigs that need it. Not medicating the entire barn helps promote the responsible use of antibiotics, Curt Haverkamp says.
Winkler, a wean-finish production manager with Haverkamp Brothers at Bern, Kan., was tired of seeing weaned pigs fall back and he sought a better way to save more of the challenged pigs in their fallback pens. The result: the Gruel-O-Matic Rescue Feeder from HavWin LLC that allows feedstuffs to be put in a feed tray, which also has nipple waterers so the piglets can mix gruel to their own desired consistency.
Spring-loaded fasteners anchor the feeder securely to the floor. There are two models: a larger model with two feed trays and four nipple waterers for each tray, and a smaller unit with two feed trays and two nipple waterers for each tray. The larger model accommodates about 50 to 60 head; the smaller unit works with 25 to 30 head.
A poly tank attached to the system can administer water, electrolytes and antibiotics to the pigs that need it. Not medicating the entire barn helps promote the responsible use of antibiotics, Curt Haverkamp says.
“Pretty simple design and pretty sturdily built,” says judge Brad Leuwerke, Swine Vet Center. “If it does what they say it does to get pigs started or help the fallbacks, there is tremendous value.”
Winkler and Haverkamp say pigs dive into the trough to get the gruel, and that the troughs are licked clean. However, judge Gary Anderson, ag engineering professor from the South Dakota State University, wants assurance that all the pigs are getting the needed gruel. “Will the runt still be getting pushed out of the way?” he asks.